تاريخ الفيزياء
علماء الفيزياء
الفيزياء الكلاسيكية
الميكانيك
الديناميكا الحرارية
الكهربائية والمغناطيسية
الكهربائية
المغناطيسية
الكهرومغناطيسية
علم البصريات
تاريخ علم البصريات
الضوء
مواضيع عامة في علم البصريات
الصوت
الفيزياء الحديثة
النظرية النسبية
النظرية النسبية الخاصة
النظرية النسبية العامة
مواضيع عامة في النظرية النسبية
ميكانيكا الكم
الفيزياء الذرية
الفيزياء الجزيئية
الفيزياء النووية
مواضيع عامة في الفيزياء النووية
النشاط الاشعاعي
فيزياء الحالة الصلبة
الموصلات
أشباه الموصلات
العوازل
مواضيع عامة في الفيزياء الصلبة
فيزياء الجوامد
الليزر
أنواع الليزر
بعض تطبيقات الليزر
مواضيع عامة في الليزر
علم الفلك
تاريخ وعلماء علم الفلك
الثقوب السوداء
المجموعة الشمسية
الشمس
كوكب عطارد
كوكب الزهرة
كوكب الأرض
كوكب المريخ
كوكب المشتري
كوكب زحل
كوكب أورانوس
كوكب نبتون
كوكب بلوتو
القمر
كواكب ومواضيع اخرى
مواضيع عامة في علم الفلك
النجوم
البلازما
الألكترونيات
خواص المادة
الطاقة البديلة
الطاقة الشمسية
مواضيع عامة في الطاقة البديلة
المد والجزر
فيزياء الجسيمات
الفيزياء والعلوم الأخرى
الفيزياء الكيميائية
الفيزياء الرياضية
الفيزياء الحيوية
الفيزياء العامة
مواضيع عامة في الفيزياء
تجارب فيزيائية
مصطلحات وتعاريف فيزيائية
وحدات القياس الفيزيائية
طرائف الفيزياء
مواضيع اخرى
LASER ION STRUCTURE
المؤلف:
Mark Csele
المصدر:
FUNDAMENTALS OF LIGHT SOURCES AND LASERS
الجزء والصفحة:
p252
22-3-2016
1803
LASER ION STRUCTURE
Because of the high current densities required in an ion laser tube, the temperature of the plasma is incredibly hot, exceeding 5000 K! Glass melts well below this point, so there are a limited number of materials available from which a plasma tube can be constructed: beryllium oxide (a ceramic) and a few high-melting-point (refractory) metals, including tungsten and graphite. In small lasers the bore is sometimes simply made from beryllium oxide, while larger lasers often use a beryllium oxide tube with graphite or tungsten disks inserted into the tube. Holes drilled in the disks form the bore of the laser where the actual discharge takes place. Additional holes around the outside of the disks are used as a gas-return path, to equalize gas pressure in the tube, since cataphoresis will serve to pump gas toward the anode (in older designs, a gas return path, often external to the tube, was provided). This should give the reader an idea of the engineering required for the relatively complex ion laser tube compared to, say, a HeNe tube.
Even with such exotic materials and construction techniques (such as inserted disks of refractory metal), the energetic plasma of a large ion laser (one with a discharge current of perhaps 30 to 40 A) can easily erode and destroy the tube material on contact. For this reason, magnetic confinement is invariably employed with large plasma tubes. The magnet is coaxial with the laser tube and is water cooled along with the plasma tube itself. Magnetic fields of about 1200 G are employed with visible lasers, which serves to confine the discharge to the center of the plasma tube, away from the tube walls (UV lasers, with higher currents, require even higher magnetic fields). In many lasers, failure of the magnet results in rapid degradation of the plasma tube. By squeezing the plasma to the center of the tube, current density is also increased, increasing the probability of pumping an ion to a high-energy state and hence increasing gain (and ultimately, output power). Generally, small air cooled lasers do not use confining magnetic fields since their discharge currents are much lower than those of large-frame ion tubes (10 A for a small tube as opposed to 40 A for a large one) as well as the physical difficulties in constructing a magnet around a ceramic tube which must have an extremely large airflow around it to avoid failure (a magnet would serve to insulate the plasma tube trapping heat). With water cooling, of course, this is not a concern.
Whereas the use of a magnetic field enhances output power, too high a magnetic field can actually impair laser output. As the magnetic field is increased, the plasma becomes more confined to the center of the bore, increasing current density and hence output power. However, there comes a point where the Zeeman effect of the magnetic field on the ion energy levels becomes significant. As the magnetic field becomes stronger, it causes the energy levels to split into many closely spaced levels. At low magnetic fields this effect serves to broaden laser output spectrally, but as the magnetic field becomes too intense, the gain curve becomes too spread out (the gain curve flattens) with many points at both edges below lasing threshold. Gain is hence wasted and the output power drops. Ion lasers have separate constant-current power supplies for these magnets, and the optimal magnetic field is dependent on the line in operation.
Unlike HeNe lasers, which utilize simple aluminum cold cathodes, heated cathodes are required in an ion laser to prolong the life of the tube. By heating the cathode, electrons are emitted from the surface, which serves to reduce the voltage drop associated with the energy required to pull electrons off the surface of the cathode. With a lower voltage drop, the power dissipated at the cathode drops; the tube runs at lower voltage and there is less damage to the cathode during operation. In most cases the heater is a small coil of tungsten wire coated with oxide to prolong life. A low voltage, around 2.5 to 3 V, at a high current of between 10 and 30 A, heats the coil. The coil itself often acts as the cathode, so the laser tube may have only three electrical connections: two for the cathode/heater and one for the anode (the positive terminal). The cathode must be preheated before initiating the discharge. Most lasers have a built-in delay, which activates the heater for 45 seconds before initiating the discharge.
Some ion laser tubes (especially older ones using graphite disks) feature tertiary electrodes in the quartz stems, extending from the tube holding the Brewster windows, such as those shown in Figure 1.1, in which the electrode is seen along with two leads connecting to the cathode. These stinger electrodes are used to generate a small charge that repels dust generated from the graphite disks, keeping it off
Figure 1.1. Stinger electrodes.
the inside surface of the window. Power is provided via a small high-voltage generator, usually inside the laser head itself. These electrodes are also used on some metal-vapor lasers, such as HeCd tubes, to help keep stray metal vapor from migrating toward the windows, where it would be deposited as an opaque film.
As an ion laser operates, it consumes gas through a process called sputtering in which energetic (and heavy) ions strike the internal tube material (both the tube and the electrodes) and are buried into the surface, effectively reducing gas pressure in the tube. As tube pressure is reduced, tube voltage drops, damage to the cathode increases, and laser output drops until it is finally extinguished. Ion lasers hence require a gas replenishment system to keep the tube pressure within a usable range. For a simple ion laser tube such as a small air-cooled type, this gas is usually replenished by means of a large ballast volume connected to the tube. This serves as a buffer to supply extra gas to the tube as required. An external ballast volume (in the form of a tank) is almost always found on krypton laser tubes since the output of these lasers is considerably more sensitive to pressure than is that of argon lasers. On many small argon laser tubes the volume of the cathode and anode is sufficient to permit them to serve as ballast volumes, but with larger ion lasers, an active-replenishment system is used which injects gas into the tube as required. The system monitors the tube pressure either by means of a vacuum gauge directly attached to the tube or by monitoring the voltage across the tube (which drops as the pressure drops). When gas is required, a system of two electromagnetic gas valves releases a small, controlled amount of gas from a high-pressure reservoir into an intermediate volume (the ready condition) and then into the tube (the fill condition). Two valves are opened in sequence (as illustrated in Figure 1.2) to increase gas pressure in controlled steps (the small intermediate volume between the valves). This arrangement ensures that the tube is not accidentally overfilled with gas from the high-pressure reservoir. While an under filled tube can simply be filled with more gas from the reservoir, an overfilled tube is usually impossible to start, and hence an expensive ion laser tube can easily be ruined by overfilling. Large krypton lasers usually employ both a large ballast volume and an active-replenishment system to help stabilize gas pressure as the laser operates.
As an example of a practical ion laser, consider the small air-cooled research laser pictured in Figure 1.3. This particular laser is housed in an acrylic box, allowing inspection of the laser components. The laser tube, seen here glowing, is terminated on either end by Brewster windows. The heated cathode is housed in the large bell shaped piece on the left and the anode on the right. The plasma tube between the electrodes, made of beryllium oxide, is shrouded in a mass of cooling fins. Some light is, however, visible between the fins and the mount; this is emanating from the intense
Figure 1.2. Ion laser gas replenishment.
Figure 1.3. Small krypton-ion laser.
light inside the translucent ceramic bore. Cooling air from a 400-ft3/min blower enters the laser from the rear, brought in through the white tube behind the laser, and blows directly through the fins to remove the over 1000 W of heat produced. On the top of the entire assembly is a large metal can connected to the anode via a flexible metal line. This serves as the gas ballast, which is quite large in this case because it is a krypton laser, in which the output of the yellow line is extremely sensitive to pressure. Cavity mirrors, as well as the tube assembly itself, are mounted on an optical rail in this case. Many commercially available air-cooled lasers are packaged in a small, compact housing with an umbilical cable connecting the laser head (containing the plasma tube, optics, and some electronics) to the main power supply. Some lasers have huge fans mounted directly atop the laser assembly, while others, like the unit pictured, use a flexible hose to connect the blower. All feature safety interlocks to ensure that airflow is adequate and/or laser temperature is not excessive, since failure of a cooling fan can cause a laser to fail in under a minute!
Figure 1.4. Typical large-frame argon-ion laser.
A large-frame ion laser (with the cover removed) is pictured in Figure 1.4 together with the remote control operator’s panel. This is a standard laboratory-type laser with a water-cooled ceramic plasma tube and magnet. The only parts of the tube that are visible are the heated cathode, in the metal can at the front of the tube, and the Brewster windows mounted on quartz stems protruding from the tube (seen here glowing brightly, with laser light scattered from the windows). In this particular laser an aperture (for mode limiting) is mounted in front of the OC on the left. The HR is mounted on a quick-change bayonet mount, allowing the user to select a multiline optic or a wavelength selector for single-line operation. The laser is powered from a separate power supply that consumes 45 A of 208 V three-phase power. The power supply, along with the laser tube/ magnet combination, is water cooled.
الاكثر قراءة في مواضيع عامة في الليزر
اخر الاخبار
اخبار العتبة العباسية المقدسة
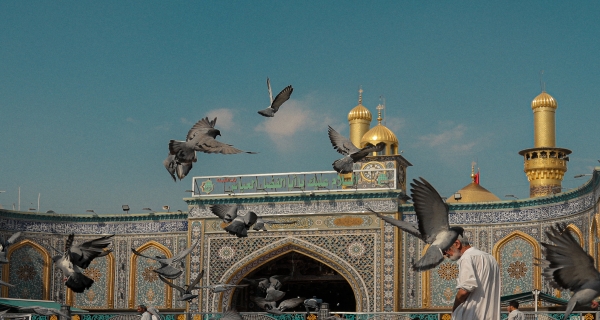
الآخبار الصحية
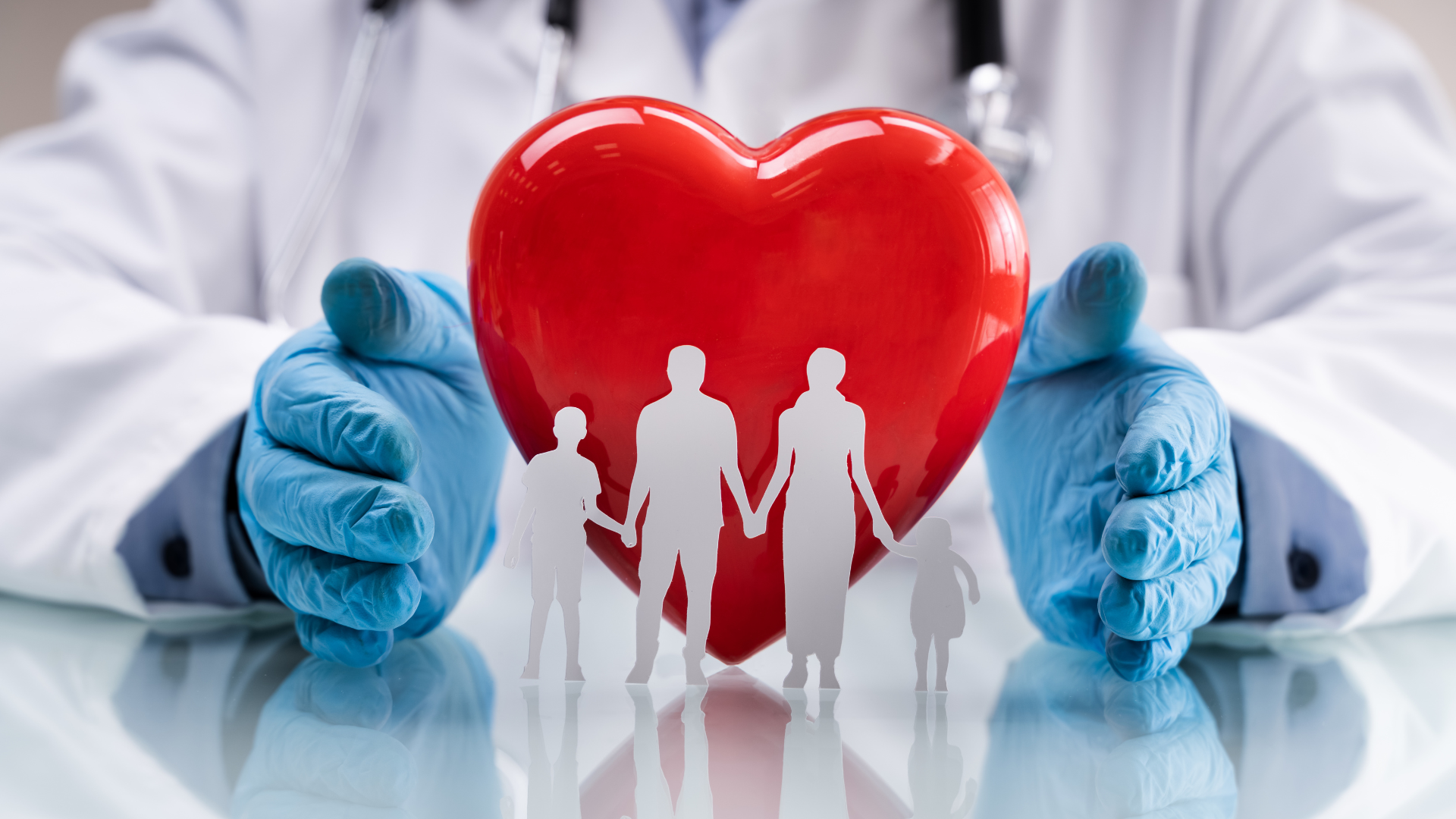